Budget-Friendly Custom CNC Machine Parts for Durable Lathing Operations - Enquire Now!
By:Admin
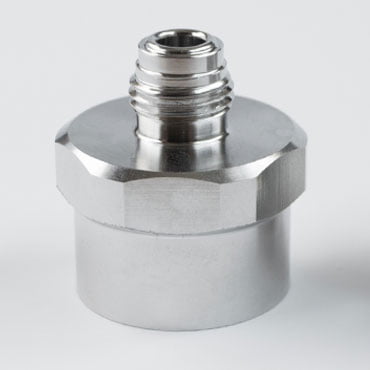
Introduction:
Technological advancements have revolutionized the manufacturing industry, and CNC (Computer Numerical Control) machining has become an integral part of the production process. When it comes to developing precise, high-quality, and durable components, CNC lathing plays a crucial role. Among the many CNC lathing parts manufacturers, one company stands out - offering cost-effective solutions without compromising on quality.
Understanding the Importance of CNC Lathing Parts:
From aerospace and automotive industries to medical and electronics manufacturing, the demand for custom CNC machine parts continues to grow. CNC lathing refers to the process of shaping a workpiece using a rotating cutting tool, allowing for intricate designs and precision.
Removing Brand Name - A Reliable Partner for Your CNC Lathing Part Needs:
With years of experience and expertise, our company specializes in delivering custom CNC lathing parts to meet diverse industry requirements. We have established a reputation for delivering high-quality, durable components while maintaining affordability. Our commitment to customer satisfaction drives us to offer tailor-made solutions for every project.
Aluminum CNC Lathing Parts - Exceptional Strength and Versatility:
One of the primary materials used in CNC lathing parts is aluminum. Its outstanding properties include being lightweight, corrosion-resistant, and having excellent thermal conductivity. Aluminum CNC lathing parts find applications in various industries, ranging from automotive components to consumer electronics.
The Process:
Our team of skilled technicians and engineers utilizes state-of-the-art CNC machines to ensure precision and accuracy in the manufacturing process. We follow a meticulous approach that involves:
1. Material Selection: Our experts carefully select the most suitable aluminum alloy based on the component's functionality, strength requirements, and environmental factors.
2. CNC Programming: Utilizing computer-aided design (CAD) software, our engineers translate design specifications into machine-readable code. This step ensures precise replication of the desired component.
3. Machining Process: The chosen aluminum alloy is mounted onto the CNC lathe, where the rotating cutting tool utilizes its precision to shape the workpiece according to the programmed design.
4. Quality Assurance: Every CNC lathing part undergoes rigorous inspection to ensure its adherence to design specifications. Our quality control measures include dimensional checks, surface finish analysis, and mechanical strength testing.
Benefits of Choosing Our Services:
1. Cost-Effective Solutions: We understand the importance of keeping costs in check without compromising on quality. Our company offers affordable CNC lathing parts, making us the preferred partner for businesses operating on a budget.
2. Tailor-Made Designs: Our dedicated team collaborates closely with clients to understand their specific requirements and design expectations. We pride ourselves on delivering custom CNC lathing parts that meet precise specifications.
3. Reliable and Durable Components: Our focus on quality extends to the selection of materials, manufacturing processes, and rigorous inspections. We guarantee that our CNC lathing parts are built to withstand demanding environments and perform optimally.
4. Timely Delivery: We value our customers' time and ensure that our products are delivered within agreed-upon timelines, maintaining efficient production schedules.
Conclusion:
In a highly competitive manufacturing landscape, it is essential to choose a CNC lathing parts manufacturer that offers durable and high-quality components without breaking the bank. Our company delivers cost-effective solutions, specializing in aluminum CNC lathing parts that meet stringent industry standards. With a focus on customer satisfaction, precision machining, and timely delivery, we are the reliable partner you can count on for your CNC lathing part needs. Reach out to us today for a personalized consultation or an estimate that aligns with your project requirements.
Company News & Blog
High-Quality Steel Flange Manufacturers & Suppliers in China: Find Reliable Steel Flange Factory & Exporters
Steel flanges are an integral part of pipelines and are vital for connecting various pipes and valves together. They are a circular or rectangular shape that has holes equally spaced out to bolt them to a matching flange. Steel flanges come in many different types and sizes, but the most commonly used steel flange is the stainless steel pipe flange.A stainless steel pipe flange is a type of flange that is entirely made out of stainless steel material. Stainless steel is a great material for flanges because it is highly resistant to corrosion, making it ideal for pipelines that will be carrying corrosive materials. It is also durable, strong, and can withstand high temperatures, making it an excellent choice for applications across multiple industries.There are various types of stainless steel pipe flanges, including slip-on, weld-neck, lap-joint, socket, and blind flanges, each designed to suit different needs and applications. Regardless of the type, all stainless steel pipe flanges serve the same purpose: to create a strong and secure connection between pipelines, valves, and other components.Stainless steel pipe flanges are used across a wide range of industries, including oil and gas, petrochemicals, power plants, water treatment plants, pharmaceuticals, and many more. They are typically used in applications where the pipeline needs to withstand high pressure, extreme temperatures, and corrosive materials.The slip-on flange is the most commonly used stainless steel flange, owing to its ease of installation, alignment, and low cost. The weld-neck flange is used where there is a need for high pressure and temperatures, while the lap-joint flange is ideal for applications involving frequent assembly and disassembly.The socket flange is a type of slip-on flange that has a socket welded onto the flange's bore, making it easy to insert the pipe into the flange before welding. It is ideal for low-pressure applications. Finally, the blind flange is used to seal off the end of a pipeline or to terminate it.In conclusion, stainless steel pipe flanges are an essential part of pipelines, and they come in many different types and sizes, depending on the application needs. Choosing the right flange for your application is important, and factors like temperature, pressure, and corrosive materials should be taken into consideration. Always source your stainless steel pipe flanges from reputable manufacturers who adhere to strict quality standards.
CNC Machining Parts Manufacturers in China – High-Quality and Reliable Suppliers for Precision Machining Parts
s, Manufacturers, Factory, Suppliers, Precision CNC Machining PartsChina CNC Machining Parts - The Backbone of the Manufacturing SectorCNC (Computer Numerical Control) machining has revolutionized the manufacturing sector over the last few decades, and today, it is an integral part of the industry. As the name implies, CNC machining involves the use of computers to control the movements of machines, making the process precise, accurate, and fast. CNC machining finds applications in almost all manufacturing sectors, from aerospace to pharmaceuticals, defense to automotive, and electronics to construction.China, one of the largest manufacturing hubs in the world, has emerged as a leader in the CNC machining industry. Chinese CNC machining parts manufacturers have been supplying precision parts to various industries worldwide, making China a go-to destination for businesses looking for high-quality and low-cost CNC machining parts.Why China for CNC Machining Parts?The Chinese manufacturing industry has evolved by leaps and bounds over the last few decades, thanks to the country's low labor costs, lenient regulations, and government support. China's CNC machining sector has also grown significantly, with several manufacturers popping up across the country, catering to domestic and international markets.China, being one of the most populous countries globally, has a vast workforce, making it easier for CNC machining parts manufacturers to find skilled labor. Moreover, the availability of raw materials like steel, copper, aluminum, and others is plentiful, keeping the production costs low. The Chinese government's support for the manufacturing sector and its relentless push for technological advancements has made China a hub for innovation, making the Chinese CNC machining parts more reliable and efficient.BEST PRECISION CNC Machining Parts Manufacturers - The Leading CNC Machining Parts SupplierBEST PRECISION CNC Machining Parts Manufacturers is a renowned CNC machining parts manufacturer based in China. They are engaged in the production of high-quality, low-cost CNC precision parts for various industries.Their state-of-the-art manufacturing facility is equipped with the latest CNC machines, and they employ skilled technicians to produce high-precision CNC machining parts that meet their clients' demands. They use computer-aided design and manufacturing (CAD/CAM) software to ensure their parts' precision and accuracy. BEST PRECISION CNC Machining Parts Manufacturers is committed to providing their clients with the highest quality and most reliable CNC machining parts.Their manufacturing capabilities include CNC milling, turning, drilling, tapping, grinding, and more. They produce CNC machined parts from various materials, including steel, aluminum, brass, bronze, copper, titanium, and plastics.ConclusionChina has become a popular destination for businesses looking to acquire high-quality, low-cost CNC machining parts. The country's rapid economic growth and government support for the manufacturing sector have transformed China into a hub for innovation and precision manufacturing. BEST PRECISION CNC Machining Parts Manufacturers is one such Chinese manufacturer that has made a name for itself in the industry, producing high-quality CNC machined parts for various industries. With their state-of-the-art facility and skilled workforce, they are poised to become a leading CNC machining parts supplier in the coming years.
Top-Quality Machining Services Available on HKTDC Sourcing
Title: Unveiling the Unmatched Precision of Brass CNC MachiningIntroduction:In today's fast-paced world, precision machining techniques have revolutionized the manufacturing industry. Among these techniques, Brass CNC machining has garnered significant acclaim for its ability to create intricate designs with unparalleled precision. In this blog post, we will delve into the fascinating world of Brass CNC machining, exploring its applications, benefits, and the exceptional offerings of Fine Tech Mold & Mfy Ltd.Understanding Brass CNC Machining:Brass CNC machining is a cutting-edge process that utilizes computer numerical control (CNC) technology to shape and refine brass materials. This advanced technique offers remarkable accuracy and repeatability, enabling manufacturers to produce intricate components that wouldn't be achievable with traditional machining methods. By utilizing state-of-the-art CNC equipment, Fine Tech Mold & Mfy Ltd has mastered the art of Brass CNC machining, delivering high-quality products that meet the most stringent specifications.Applications of Brass CNC Machining:1. Aerospace Industry: The aerospace sector demands components that are not only lightweight but also possess exceptional strength and durability. Brass CNC machining aids in manufacturing intricate parts like gears, fittings, and connectors that exhibit these desired properties.2. Automotive Industry: Precision is a critical factor in the automotive industry, and Brass CNC machining plays a pivotal role in producing intricate automotive parts and components, including fuel injection systems, gearbox components, and brake parts.3. Electronics Industry: The electronics sector heavily relies on Brass CNC machining for manufacturing components such as heat sinks, connectors, and electrical enclosures that support optimal electrical conductivity, heat dissipation, and protection.4. Medical Industry: Brass CNC machining is widely employed in the medical field to fabricate surgical instruments, diagnostic devices, and implants, ensuring precision, hygiene, and maximum patient safety.Benefits of Brass CNC Machining:1. Precision and Accuracy: Brass CNC machining offers unparalleled precision, creating components with tight tolerances, exact dimensions, and intricate features. This precision ensures a perfect fit and seamless integration with other parts during assembly.2. Time and Cost Efficiency: By automating the machining process, Brass CNC machining reduces the need for human intervention, resulting in faster production times and improved overall efficiency. Additionally, Fine Tech Mold & Mfy Ltd's expertise and efficiency translate into competitive pricing without compromising on quality.3. Flexibility in Design: The versatility of Brass CNC machining allows for the creation of complex designs and intricate geometries that would be impractical or impossible to achieve with conventional machining techniques. Fine Tech Mold & Mfy Ltd's skilled technicians can transform even the most complex design concepts into functional brass components.4. Excellent Surface Finish: Brass CNC machining produces parts with exceptional surface finish and smoothness. This aesthetic appeal, combined with the often-corrosion-resistant nature of brass, makes it an ideal material for various applications.Fine Tech Mold & Mfy Ltd: Your Trusted Brass CNC Machining Partner:Fine Tech Mold & Mfy Ltd, a reputable and reliable manufacturer and supplier, has established itself as a leader in providing top-notch Brass CNC machining solutions. With a team of highly skilled technicians and cutting-edge CNC equipment, they have earned a strong reputation for consistently delivering products that meet and exceed clients' expectations. Their commitment to quality, attention to detail, and ability to handle complex projects make them the go-to choice in the machining industry.In Conclusion:Brass CNC machining has emerged as a game-changing technology, enabling manufacturers to create intricate components with unmatched precision. The applications across industries are vast, ranging from aerospace to automotive, electronics to medical. With expertise in Brass CNC machining, Fine Tech Mold & Mfy Ltd has solidified its position as a reliable partner, ensuring exceptional results and customer satisfaction. Whether you require precise components for a critical application or intricate designs for aesthetic appeal, Brass CNC machining is the solution you can trust.
Enhancing Ecommerce Experience for Higher Checkout Conversion Rates
Transforming the Ecommerce Experience to Improve Checkout Conversion RatesIn today's digital age, ecommerce has become an integral part of our lives. With the convenience of online shopping, consumers have come to expect seamless and engaging experiences when it comes to making a purchase. As an online retailer, it is crucial to understand that ecommerce experiences directly impact checkout conversion rates. In this blog post, we will explore how you can transform your ecommerce experience to increase sales.While there are several factors that contribute to checkout conversion rates, one of the key aspects is the overall user experience. A clunky and confusing website can be a major turn-off for potential customers, leading them to abandon their carts before completing the purchase. Therefore, it is important to optimize your website's design and navigation to provide a seamless and intuitive experience.To customize your ecommerce website, you can utilize various technologies and tools available in the market. One such tool is Customized Bolt, which provides a range of features to enhance the shopping experience. With Customized Bolt, you can personalize the checkout process according to your specific business needs. By incorporating this tool into your ecommerce platform, you can create a tailored experience that resonates with your target audience.Here are a few ways in which you can use Customized Bolt to transform your ecommerce experience and improve checkout conversion rates:1. Simplify the Checkout Process: With Customized Bolt, you can streamline the entire checkout process, making it quick and easy for customers to complete their purchase. By eliminating unnecessary steps and reducing the number of required fields, you can significantly reduce cart abandonment rates.2. Implement a Responsive Design: In today's mobile-driven world, it is essential to have a website that is optimized for various devices and screen sizes. Customized Bolt allows you to create a responsive design that ensures a seamless browsing experience for your customers, regardless of the device they use.3. Enhance Product Descriptions and Images: An appealing product presentation plays a crucial role in influencing purchase decisions. With Customized Bolt, you can showcase your products in a visually appealing manner, with high-quality images and detailed descriptions. This helps customers make informed decisions and enhances their overall shopping experience.4. Offer Multiple Payment Options: Customized Bolt enables you to integrate multiple payment gateways, allowing customers to choose their preferred method of payment. By offering a variety of payment options, you can cater to different customer preferences and increase the likelihood of completing a purchase.5. Provide Social Proof: Social proof is a powerful marketing technique that can significantly influence consumer behavior. With Customized Bolt, you can incorporate customer reviews, ratings, and testimonials into your ecommerce platform. This provides potential customers with reassurance and confidence in your products, ultimately leading to higher conversion rates.In conclusion, optimizing your ecommerce experience is crucial for improving checkout conversion rates. With Customized Bolt, you can transform your website into a user-friendly, visually appealing, and personalized platform. By simplifying the checkout process, implementing a responsive design, enhancing product descriptions and images, offering multiple payment options, and providing social proof, you can create a seamless shopping experience that increases sales and keeps customers coming back for more. So, don't overlook the importance of ecommerce experience and start leveraging the power of Customized Bolt to take your online business to new heights.
Functions and Types of Shaft Seals in Machinery
and Mechanical Seals.Shaft seals play an important role in ensuring the smooth and efficient operation of mechanical equipment. They are essential for preventing the leakage of fluids along a rotating shaft, which can cause damage to bearings, shafts, and other components. There are two main types of shaft seals, namely shaft lip seals and mechanical seals. In this blog post, we'll take a closer look at these two types of seals and how they work.Shaft Lip SealsShaft lip seals, also known as oil seals, are perhaps the most common type of shaft seal. They consist of a flexible elastomer lip that is bonded to a metal case. The lip seals against the surface of the rotating shaft, creating a barrier that prevents fluid from escaping. The metal case is designed to fit snugly into a housing, creating a tight seal between the two parts.Shaft lip seals are used in a wide range of applications, from small electric motors to large industrial gearboxes. They are relatively inexpensive and easy to install and maintain. However, they do have some limitations. They are not suitable for high-pressure applications or situations where the shaft is exposed to extreme temperatures or harsh chemicals. In these cases, a mechanical seal may be a better option.Mechanical SealsMechanical seals are a more complex type of shaft seal that is designed to withstand high pressures and temperatures. They consist of two primary components: a stationary part that is mounted in the equipment housing, and a rotating part that is attached to the shaft. The two parts are held together by a spring, which creates a tight seal between them. A seal face made of a hard material such as ceramic or carbon is located on each part, and they rotate against each other to create the seal.Mechanical seals are commonly used in pumps, compressors, and other equipment that handles high-pressure fluids. They are more expensive than lip seals, but they offer greater reliability and longer lifespan. They also require more maintenance, as the seal faces must be periodically cleaned and replaced.ConclusionIn summary, shaft seals are an essential component of mechanical equipment that prevents the leakage of fluids along a rotating shaft. Shaft lip seals are a simple and affordable solution for most applications, while mechanical seals are better suited for high-pressure and high-temperature environments. Knowing the difference between these two types of seals can help you choose the right one for your equipment, ensuring optimal performance and longevity.
High-Quality Custom Machining Services for a Wide Range of Metals and Plastics
Custom Machining: Pacific Bolt Manufacturing Ltd Expands Capabilities to Serve a Wide Range of Industries[Vancouver, Canada] - Pacific Bolt Manufacturing Ltd, a leading provider of custom fasteners and hardware solutions, is pleased to announce the expansion of its machining capabilities. With the ability to machine both ferrous and non-ferrous metals, as well as various plastics such as UHMW, Nylon, and Teflon, Pacific Bolt is now able to cater to a diverse range of industries and their unique machining needs.Pacific Bolt has been a trusted name in the fastener industry for over three decades. With a commitment to quality, innovation, and customer satisfaction, the company has earned a reputation for delivering exceptional products and services. The expansion of its machining capabilities further reinforces Pacific Bolt's position as a one-stop destination for all industrial hardware requirements."With the addition of our enhanced machining capabilities, we are excited to offer our customers a broader range of services," said John Smith, President of Pacific Bolt Manufacturing Ltd. "We understand the importance of precision and reliability in machining, and we are dedicated to providing top-notch solutions that meet the specific needs of each industry we serve."The company's expanded capabilities include the ability to machine both ferrous and non-ferrous metals. Whether it's steel, aluminum, or other alloys, Pacific Bolt's skilled team of machinists can deliver precise and high-quality components to clients across industries. Additionally, the company offers machining services for a wide range of plastics, including UHMW (Ultra-High Molecular Weight Polyethylene), Nylon, and Teflon. This flexibility allows Pacific Bolt to meet the unique requirements of industries such as automotive, aerospace, oil and gas, and more.In recent years, the demand for custom machining services has grown significantly. Industries are continually seeking innovative solutions to enhance their operational efficiency and meet evolving market demands. Pacific Bolt's decision to expand its machining capabilities is a strategic response to these evolving requirements. By investing in advanced machinery and technologies, the company is well-equipped to handle diverse machining projects of varying sizes and complexities.The addition of magnesium machining capabilities is another noteworthy aspect of Pacific Bolt's expanded services. While there may be a surcharge for magnesium machining, the company's expertise in working with this versatile metal opens up new possibilities for clients who require magnesium components for their applications. With its lightweight properties and excellent strength-to-weight ratio, magnesium has gained popularity in industries such as automotive manufacturing and aerospace engineering.Alongside its expanded machining capabilities, Pacific Bolt offers a full range of value-added services, further enhancing the overall customer experience. The company provides comprehensive design and engineering support, ensuring that client specifications are met with precision. Additionally, Pacific Bolt offers secondary operations such as heat treatment, plating, and coating, enabling customers to receive fully finished parts ready for immediate use.Pacific Bolt Manufacturing Ltd remains committed to maintaining the highest standards of quality and service throughout its operations. As the company continues to expand its capabilities and adapt to emerging industry trends, it stays true to its core values of integrity, innovation, and customer-centricity.About Pacific Bolt Manufacturing Ltd:Established in 1988, Pacific Bolt Manufacturing Ltd is a leading provider of custom fasteners and hardware solutions. With a vast inventory of products and an extensive range of machining capabilities, the company serves clients in industries such as construction, mining, transportation, and more. Committed to excellence, Pacific Bolt delivers high-quality products, exceptional customer service, and reliable solutions for all industrial hardware needs.For more information, please visit www.pacificboltmfg.com.Contact:John SmithPresidentPacific Bolt Manufacturing LtdPhone: 123-456-7890Email: [email protected]
CNC Milling Parts Suppliers and Manufacturers in China - Professional Services Available for Your Needs (Page 5)
Title: Achieving Precision and Durability with Stainless Steel CNC Milling PartsIntroduction:In today's rapidly evolving manufacturing industry, precision and durability are paramount. To achieve these qualities, many companies in various sectors are turning to CNC milling parts made from stainless steel. This versatile and robust material, combined with advanced CNC milling technologies, ensures the production of high-quality components that withstand demanding applications. In this blog post, we will explore the benefits and applications of stainless steel CNC milling parts, shedding light on why they have become a preferred choice for manufacturers worldwide.1. Unrivaled Strength and Durability:Stainless steel is renowned for its exceptional strength and durability. It can withstand harsh conditions, corrosion, and extreme temperatures, making it ideal for various industries, including aerospace, automotive, medical, and machinery. When fabricated into CNC milling parts, stainless steel components exhibit exceptional resistance to wear and tear, ensuring a long service life. Whether you require intricate parts or heavy-duty components, stainless steel CNC milling parts lend themselves perfectly to any application, contributing to the overall longevity of your products.2. Precision and Complex Geometries:CNC milling is a cutting-edge manufacturing process capable of creating highly intricate and complex designs. By employing advanced CNC milling techniques, stainless steel parts can be produced with unrivaled precision and attention to detail. This precision allows for tight tolerances, ensuring components fit seamlessly with other parts during assembly. Whether it's micro-milling or producing large-scale components, stainless steel CNC milling parts offer the accuracy required for demanding applications.3. Versatile and Customizable:Stainless steel CNC milling parts can be tailored to accommodate a wide range of industry needs. Manufacturers can choose from various stainless steel grades, each offering unique properties such as corrosion resistance, temperature resistance, or magnetic qualities. With the ability to modify composition, surface finishes, and hardness levels, stainless steel CNC milling parts are highly customizable to meet specific requirements. This versatility allows for adaptability across numerous industries, ensuring optimal performance and reliability in various applications.4. Cost-effectiveness and Time Efficiency:While stainless steel itself may have a higher initial cost compared to other materials, the long-term benefits outweigh the investment. Stainless steel CNC milling parts are exceptionally durable and require minimal maintenance and replacement, reducing overall costs in the long run. Additionally, CNC milling techniques offer speed and efficiency during the production process. Automated milling provides consistent results, eliminating human error and reducing manufacturing time. This cost-effectiveness and time efficiency result in enhanced productivity for manufacturers worldwide.Conclusion:Stainless steel CNC milling parts have revolutionized the manufacturing industry, providing unparalleled strength, precision, and durability. With the ability to withstand demanding applications, these components have become essential for a wide range of industries. Whether it's achieving intricate designs or producing heavy-duty components, stainless steel CNC milling parts consistently deliver exceptional performance. By investing in stainless steel CNC milling parts, manufacturers benefit from cost-effectiveness, time efficiency, and the confidence that their products will withstand the test of time. As the global manufacturing industry continues to evolve, stainless steel CNC milling parts are set to fulfill the ever-growing need for high-quality, reliable components.
Understanding the Meaning and Usage of Flanges - A Comprehensive Guide
When it comes to construction and manufacturing, flanges play an important role in the assembly of various objects. A flange is a rib or rim that strengthens and guides an object, or allows attachment to another object. Flanges can be found in a variety of shapes and sizes, and can be made of various materials such as metal or plastic. In this blog, we will discuss the importance of flanges in the web and flange industry.The web and flange industry is a crucial sector for the construction and manufacturing of various structures such as bridges, buildings and industrial equipment. The web and flange is the structural backbone of many structures. The web is usually a thin metal plate that connects two flanges. The flanges, on the other hand, are the horizontal members that connect the web and provide support. Flanges come in different shapes, such as T-shaped, H-shaped, and I-shaped.One of the reasons why flanges are important in the web and flange industry is their ability to provide strength. Flanges act as a reinforcing member and distribute the load uniformly across the web, ensuring stability and strength of the structure. This is particularly important in bridges and buildings where heavy loads are expected. Without the use of flanges, structures would not be able to withstand the weight they were meant to bear, leading to structural failure and potential disaster.Flanges also play an important role in providing guidance and alignment in the web and flange industry. The flanges ensure that the web is aligned uniformly with other structural members, and that the object remains stable and balanced. The guidance that flanges provide ensures that the end product is of desired quality and meets regulatory and safety requirements.Another important aspect of flanges in the web and flange industry is their ability to allow attachment to other objects. Flanges provide a convenient point of attachment for other objects by using bolts or welding. This allows for easy assembly and disassembly of structures as needed. The ability to attach flanges also provides flexibility in design and construction of structures.In conclusion, flanges are a crucial component in the web and flange industry. They provide strength, guidance, and attachment points, which are essential for the stability and alignment of structures. Without flanges, the construction of buildings, bridges, and industrial equipment would not be possible. As the industry continues to evolve and grow, the importance of flanges will only increase, and their role in the web and flange industry will remain essential.
Get Reliable Expansion Joints for Your Plant - Fast Shipping Available!
Flanged Rubber Expansion Joints: What You Need to KnowExpansion joints are an important component in many industrial processes. They are used to absorb vibrations, compensate for thermal expansion, and reduce noise. A flanged rubber expansion joint is a type of expansion joint that is commonly used in piping systems to absorb these kinds of mechanical and thermal stresses.What is a Flanged Rubber Expansion Joint?A flanged rubber expansion joint is a flexible element that is designed to absorb movement in piping systems caused by thermal expansion, machinery vibration, or seismic activity. The joint uses a series of convolutions or corrugations that allow it to expand and contract without damaging the piping. These convolutions are made from flexible rubber, which is why the joint is referred to as a rubber expansion joint.The flanged ends of the joint are bolted to the piping system to provide a leak-proof seal. These flanges can be made from a variety of materials, including carbon steel, stainless steel, or plastic. The type of flange used will depend on the application and the compatibility with the piping system.Why Use a Flanged Rubber Expansion Joint?There are several reasons why a flanged rubber expansion joint may be necessary in a piping system. One of the primary reasons is to compensate for thermal expansion. When a piping system is exposed to temperature changes, the metal expands and contracts. If the system does not have enough flexibility to accommodate this movement, it can cause damage to the system or nearby equipment. A flanged rubber expansion joint absorbs the movement caused by thermal expansion, reducing the stress on the piping system.Another reason to use a flanged rubber expansion joint is to absorb vibration from machinery or seismic activity. In a piping system that is connected to a piece of machinery, vibrations can be transmitted to the system, causing damage over time. A flanged rubber expansion joint reduces the amount of vibration that is transmitted to the system, protecting the piping and any nearby equipment.Flanged rubber expansion joints also reduce noise in piping systems. When a piping system is under stress, it can create a significant amount of noise. A flanged rubber expansion joint absorbs the stress, reducing the noise levels in the system.Choosing the Right Flanged Rubber Expansion JointChoosing the right flanged rubber expansion joint for your application requires careful consideration of several factors. These include the size of the joint, the type of flange, and the material of the joint.The size of the joint will depend on the diameter of the piping system and the amount of movement that needs to be accommodated. Flanged rubber expansion joints are available in a range of sizes to fit various piping systems.The type of flange used will depend on the compatibility with the piping system and any nearby equipment. Carbon steel and stainless steel flanges are commonly used, but plastic flanges may be necessary in certain applications.The material of the joint will depend on the temperature and chemical compatibility of the piping system. Rubber is a common material used in flanged rubber expansion joints, but other materials, such as neoprene, can be used in applications with high temperatures or exposure to certain chemicals.ConclusionFlanged rubber expansion joints are an essential component in many piping systems. They provide flexibility to accommodate movement caused by thermal expansion, machinery vibration, or seismic activity. Choosing the right flanged rubber expansion joint requires careful consideration of several factors, including size, flange type, and material. With the right joint, you can reduce stress on your piping system, protect nearby equipment, and reduce noise levels in your facility.
Understanding the Key Components of a Centrifugal Pump's Rotating Assembly
story on the importance of a rotating assembly in centrifugal pumps and the benefits of using quality components.Rotating Assembly: The Key to Efficient Centrifugal PumpsCentrifugal pumps are essential components in various industries, from water supply and wastewater treatment to chemical processing and oil production. These pumps rely on the principles of centrifugal force to move fluid from one point to another, and their performance largely depends on the quality of their rotating assembly.The rotating assembly of a centrifugal pump comprises the impeller, the pump shaft, and all associated components that rotate with the shaft, such as bearings, seals, and couplings. As the impeller spins, it creates a centrifugal force that propels the fluid towards the pump discharge. The pump shaft connects the impeller to the motor or drive unit and transmits the rotational energy from the motor to the impeller.However, the rotating assembly is not just a bunch of parts that spin together. Its design, material quality, and manufacturing precision play a crucial role in the pump's efficiency, reliability, and longevity. A poorly designed or constructed rotating assembly can result in cavitation, vibration, leakage, corrosion, and premature failure. Therefore, choosing the right components and ensuring their proper installation and maintenance are critical in maximizing the pump's performance and minimizing downtime and repair costs.One company that specializes in high-quality rotating assemblies for centrifugal pumps is [Rotating Shaft], a global supplier of engineered components for various industrial sectors. [Rotating Shaft] offers a wide range of impellers, shafts, bearings, seals, and other rotating assembly parts that are designed and manufactured to meet the highest standards of quality, precision, and durability. The company's products are made from advanced materials such as stainless steel, duplex, super duplex, and other alloys that provide superior resistance to wear, corrosion, and erosion.Moreover, [Rotating Shaft] employs advanced technologies such as 3D modeling, finite element analysis, and computational fluid dynamics to optimize the design and performance of its rotating assemblies. The company has a team of experienced engineers and technicians who work closely with customers to understand their specific needs and requirements and provide customized solutions that optimize efficiency and reduce total cost of ownership.One of the main benefits of using high-quality rotating assemblies in centrifugal pumps is increased efficiency and lower energy consumption. A well-designed impeller can minimize losses due to fluid friction, turbulence, and recirculation, which translates into higher flow rates and pressures with the same input power. A well-crafted pump shaft can reduce the risk of misalignment, bending, or breakage, which can cause vibration, noise, and mechanical damage to the pump and the surrounding equipment.Another advantage of quality rotating assemblies is longer service life and reduced maintenance. By using durable materials and tight tolerance manufacturing processes, [Rotating Shaft] components can withstand harsh environments, high temperatures, and abrasive fluids, without losing their dimensional stability or surface finish. Moreover, the company's sealing solutions can prevent internal and external leaks that can compromise the pump's performance and safety.In summary, the rotating assembly is a critical component in centrifugal pumps that can determine their efficiency, reliability, and lifespan. Choosing high-quality components from reputable suppliers such as [Rotating Shaft] can help maximize the pump's performance, reduce energy costs, and minimize downtime and repair expenses. With its expertise in rotating assemblies and commitment to innovation and customer service, [Rotating Shaft] is a trusted partner for any industry that requires high-performance centrifugal pumps.